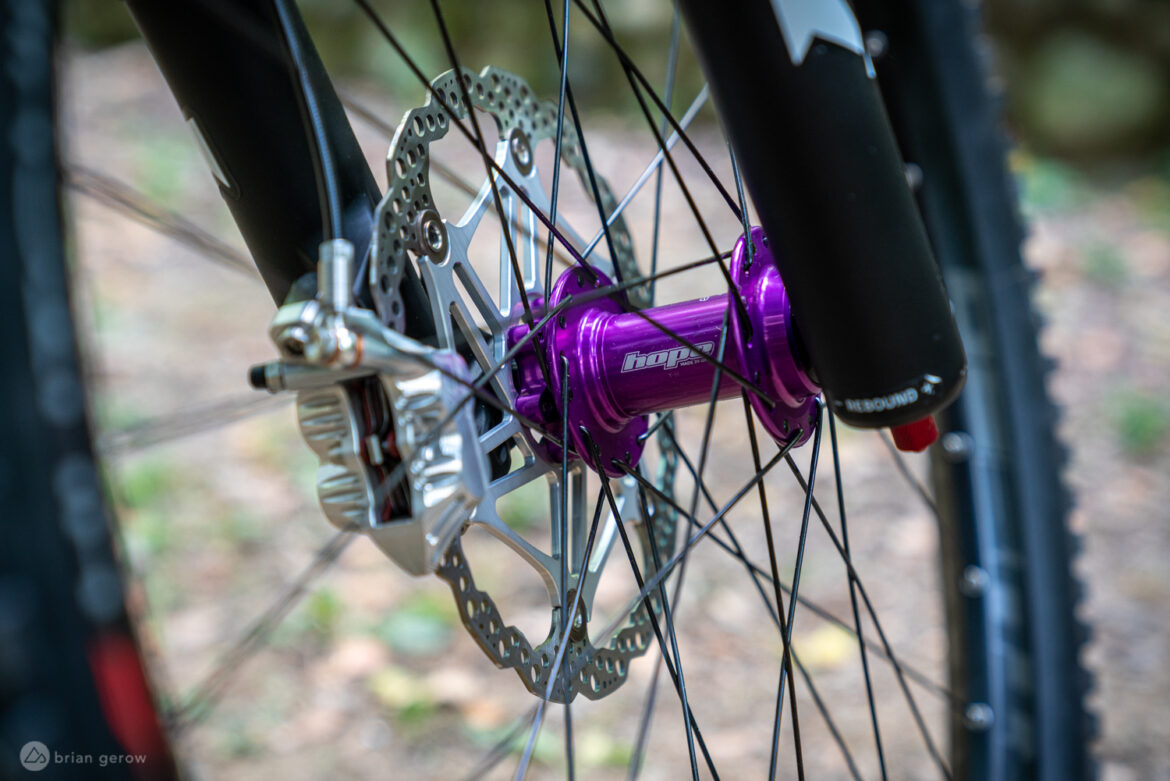
Nearly every business across the bike industry has been meaningfully affected by the Coronavirus pandemic in some way. Some, like Trust Suspension, have been forced to close the doors indefinitely, while most others are selling bikes, apparel, and components as quickly as they can produce them. The boom of folks buying bikes as a means of exercising at a distance continues, and we wanted to share the story of how a few brands are dealing with the influx.
A friend in Portland, Oregon, mentioned that while her next door neighbors were preparing to move to the east coast they put six bikes up for sale on Craigslist. The whole sixpack was sold before lunchtime rolled around. We chatted with Robin Godden at Hope Technology about how their component and frame factory has fared through the virus storm.
When the pandemic first hit, what did Hope change to keep workers safe?
Straight from the outset in late February we put in place social distancing protocols as well as an increased cleaning schedule around the factory.
At what point did you all decide to close up shop and have workers remain at home?
We decided to start to wind down production around the end of March as the COVID situation in the UK was getting worse. And [we] actually closed the factory for three weeks but, gradually brought staff back after modifications to the factory and working practices over the course of the next three months.
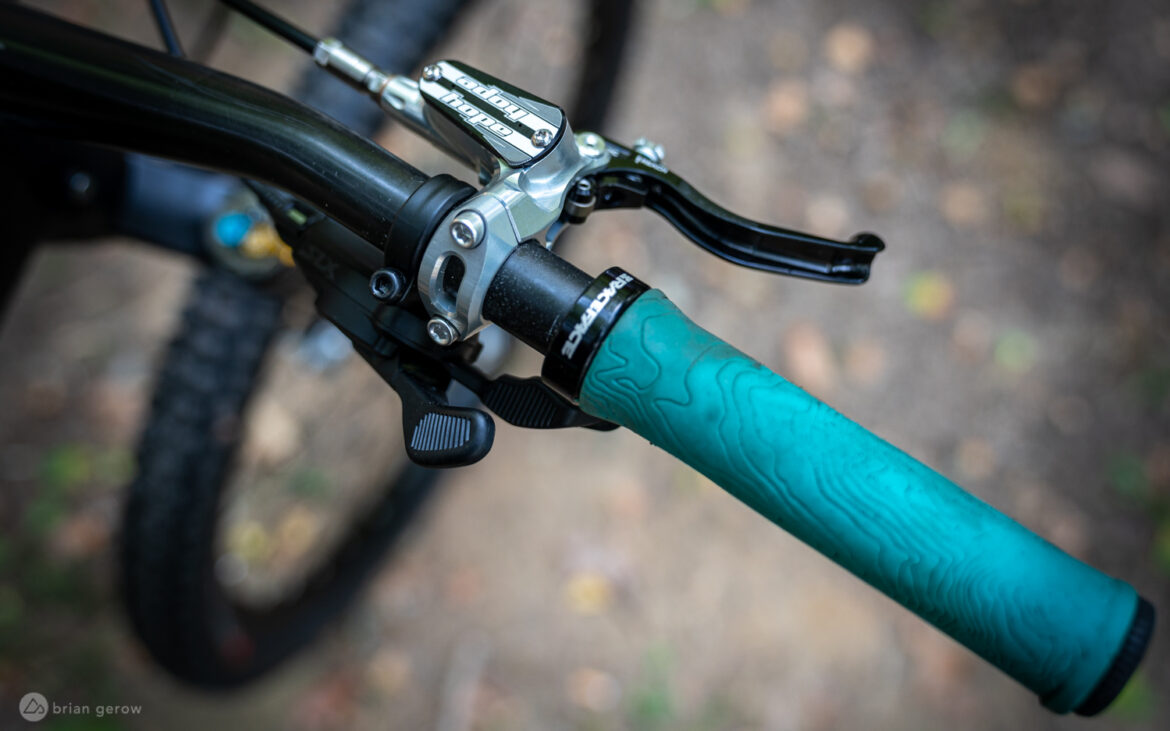
How did that lockdown affect business?
Initially, business was affected as many large customers canceled orders, but then within a few weeks of lockdown and the promotion of cycling as a form of exercise meant those orders were reinstated and increased significantly.
What’s different about working at Hope during the pandemic?
We’re actually in a really good position. We run a minimal staffing in the machine shop, due to the CNC machines, so socially distancing isn’t an issue there. We have had to re-jig the workspaces in the assembly areas for social distancing though. Throughout the factory we have implemented a one way systems and increased our cleaning protocols too.
Are you having any trouble getting raw materials or any of the small parts that might be made elsewhere?
Luckily, we had previously increased our stocks due to Brexit fears, so didn’t have any issues there. Our Italian material supplier was initially significantly affected but by the time we needed stocks they were back up and running.
And even though customers were cancelling orders we didn’t cancel a single order for raw materials.
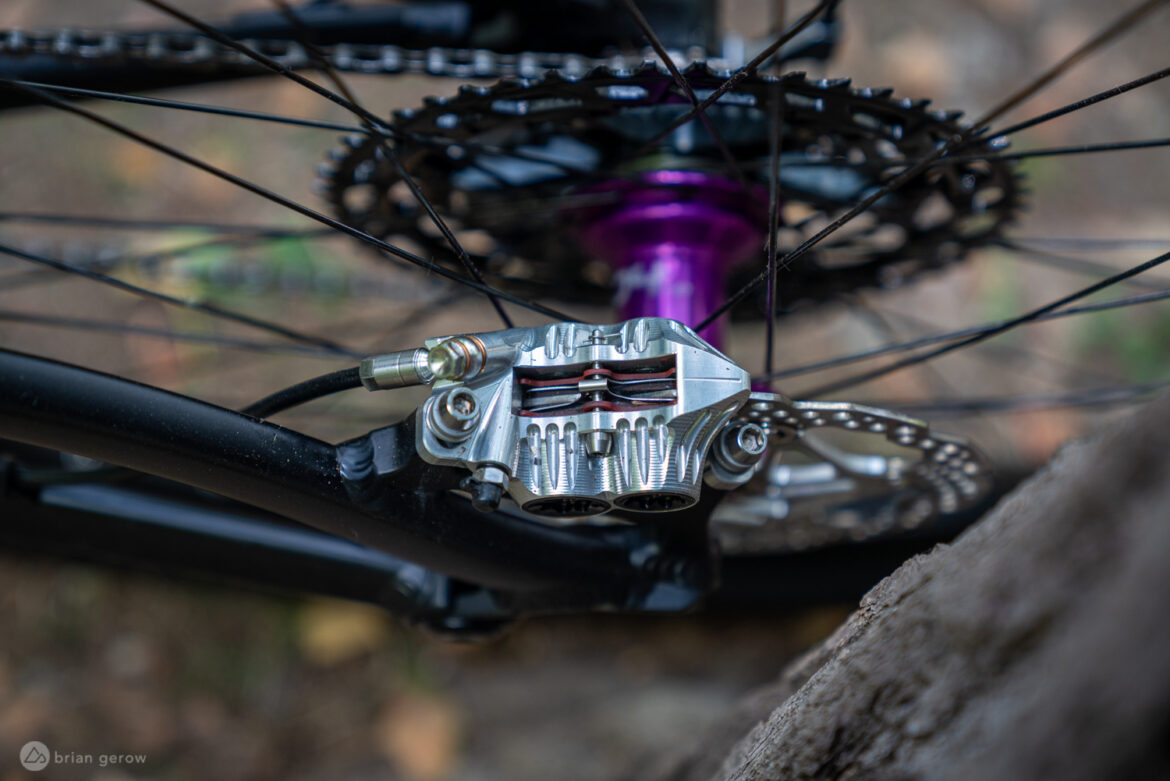
How has the recent “bike buying boom” affected Hope?
Unlike other brands, we manufacture everything in house which means we can’t just go out and find new suppliers to increase production. Instead we are investing in new machines (spending £750,000 on machines in the last month) to expand gradually and slowly increase production.
You all work with large companies like Chain Reaction as well as smaller bike shops. Are you working with your distribution networks and shops differently now?
Not much has changed with the way we work with our distribution networks. Due to the increased demand of products we have rationed parts to all shops and lead times have increased: three weeks for machined parts and six weeks for wheels, but obviously with the new machines we are increasing production to shorten lead times.
Where is the bike building process at right now? Are you all able to build complete bikes, or is that process different?
The HB building process hasn’t been affected, as it’s always been a smaller part of the business.
Without Eurobike and other tradeshows, do you all plan to share the news with riders and journalists differently during the pandemic?
Totally, obviously with the pandemic we are working on new ways to share news and showcase our products with journalists, online and on any of our channels.
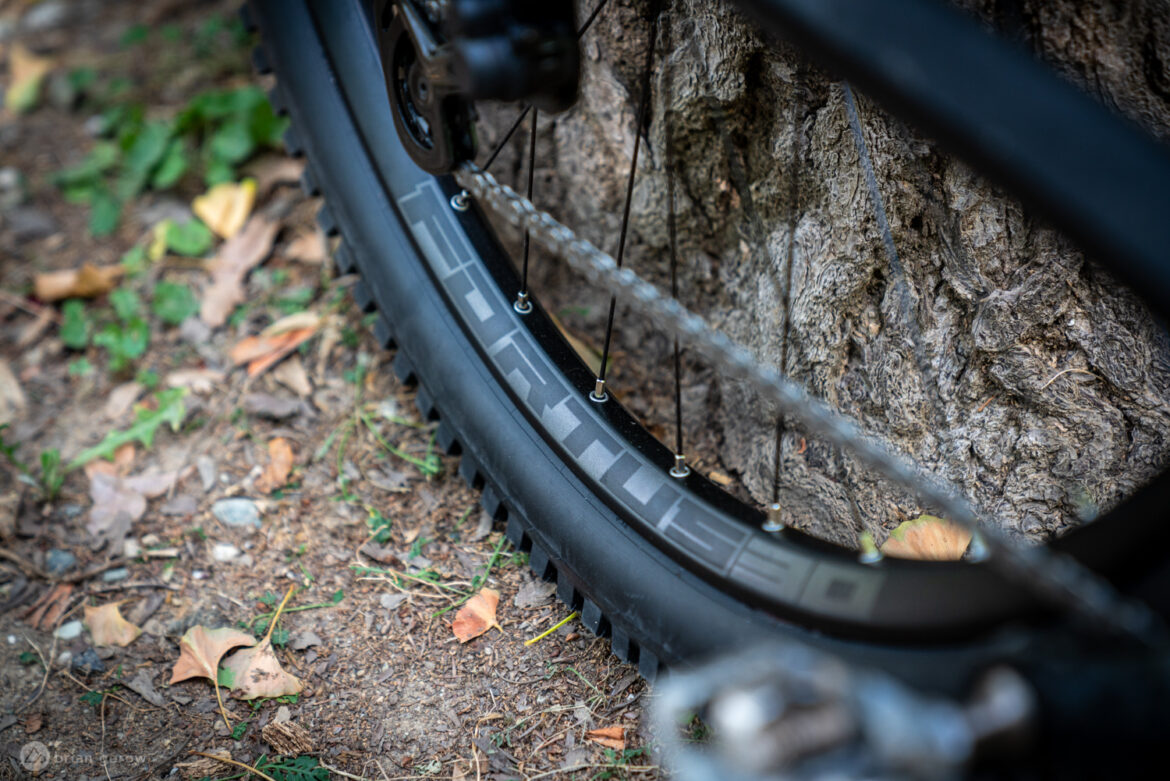
Are you all able to hold any events, like the Hope Women’s Enduro or weekly rides?
Unfortunately, we have had to cancel all our events and group rides for obvious reasons especially as we’re now in one of the areas under special measures.
Do you have a sense of when/if things will return to the former production and R&D rhythm in the factory?
At the moment we’ve put all product launches on pause, due to being at capacity producing existing products, but we’re still developing products and hope to be back in a normal rhythm by around Christmas.
Has Hope been able to maintain the majority of the workforce?
Yes, 100% of the work force – we’re actually hiring new people!
Have you all started up any fun activities or rituals that make working through the quarantine more pleasant?
Not exactly, but due to the being at capacity in the factory, more staff are doing slightly different roles, which has led to better appreciation of what other members of staff do.
Look for other interviews with industry professionals in the coming weeks, and that full review of the Fortus 30 wheels, Pro 4 Hubs, and Tech 3 V4 brakes sometime in autumn.

0 Comments