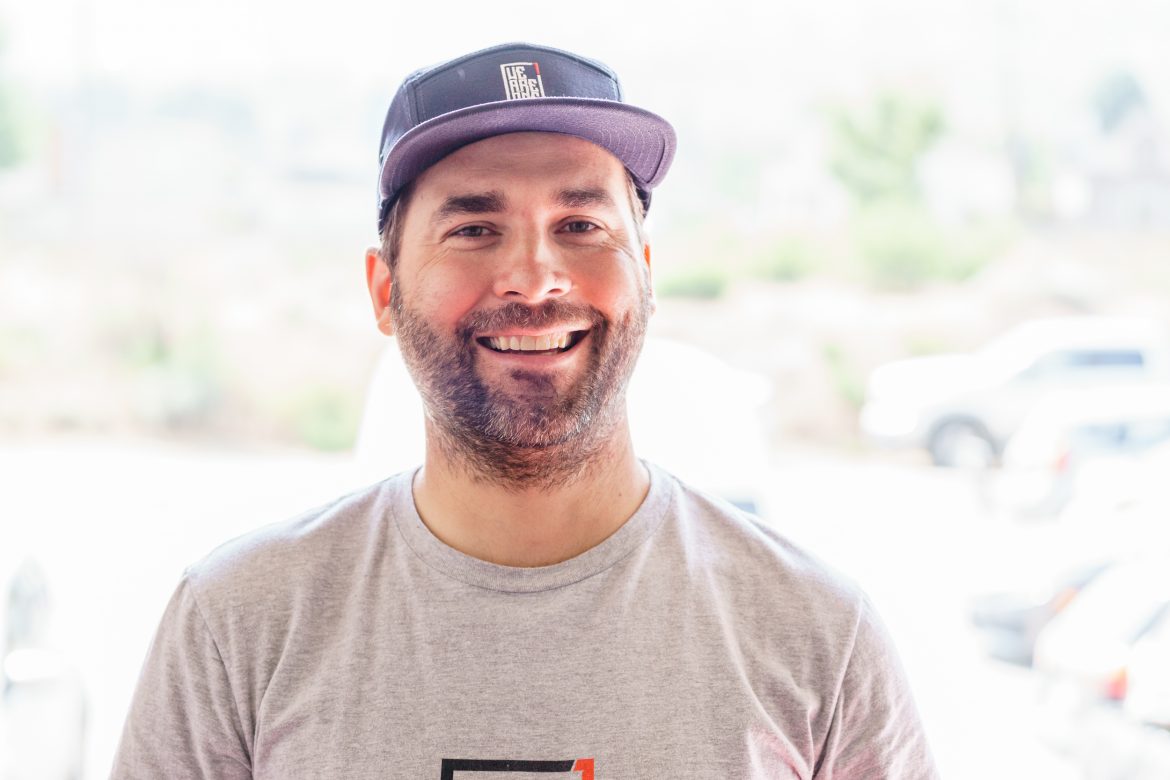
Given their often similar weights, why should I purchase carbon mountain bike rims instead of the less expensive aluminum ones? This is one of the primary questions we hoped to answer while chatting with Dustin Adams, CEO of We Are One Composites. The British Columbia factory currently makes five distinct carbon rims for varied disciplines, a unique sleeved carbon handlebar and alloy stem, and there’s a sleek new carbon full suspension frame in the works. Adams provided some clear answers to our carbon quandary and loads of other intriguing info about his Canada-made brand.
Adams’ path to Chief Executive Officer of a carbon fiber factory was like riding good singletrack; super rough with plenty of quick decisions to make, and the straightest line wasn’t always the fastest. After winning Canadian National Championships several times, and taking the top honors as the fastest North American downhiller, it’s safe to say he knows how to push gravity components to their limit. He had been racing downhill professionally for several years when he was struck by a car in 2003. After being hit Adams stopped riding bikes and fell into the deep, dark mental health chasm that often follows such an abrupt shift in ability and enjoyment. Mountain bikes and racing are who he is, and he lost that for a time.
“In high school, we did career and personal planning where we had to develop a plan of what we wanted to do after school and my three options were all ‘professional mountain bike racer.’ I was told I couldn’t be that, and I failed the course. A number of years later I went back and kinda shoved it in the teacher’s face. I was a pro when I left high school but wasn’t getting paid. Then, eventually being paid, I kind of received my dream.” Adams rode for Giant through the early nineties on their US Factory team.
During his break from bikes, Adams started a concrete company, then a successful custom-countertop business, eventually losing interest and selling off both to take an eight-month-long vacation in southeast Asia with his family. “During that trip, I figured that my duty was to get back into the cycling industry somehow. We made the decision to move from Kamloops to Squamish. I immersed myself in the riding community. It was pretty small at the time, but it was booming toward what it is now. It was a really healthy scene. I was able to just ride and do my thing, and fall back in love with it the way I wanted to.”
“Then I stumbled across an ad on Facebook from an old customer of mine who was looking for a production manager. It was Nobl Wheels. I came to the conclusion that it wasn’t the best situation to take the job. I was better suited to buy into the company. So I became a partner at Nobl in late 2015. Then I started charging hard with them. I was in Asia, learning the ins and outs of the brands and products. In 2016 we had a disagreement on a few things. My focus was to become a manufacturer because that’s my background. I didn’t see a reason to keep pushing private label products, just putting a sticker on and doing very little R&D at the factory. I didn’t see that as being the way for longevity. We couldn’t come to an agreement […]. So In early 2017, I started up We Are One.”
The company has been focused on 100% Canadian manufacturing since. Adams had seen the flaws in carbon production, quality, and the poor working conditions that accompany the faster and cheaper methods of carbon production, and he wanted to have control of the process to ensure We Are One rims come out dialed every time. Let’s dig into the details.
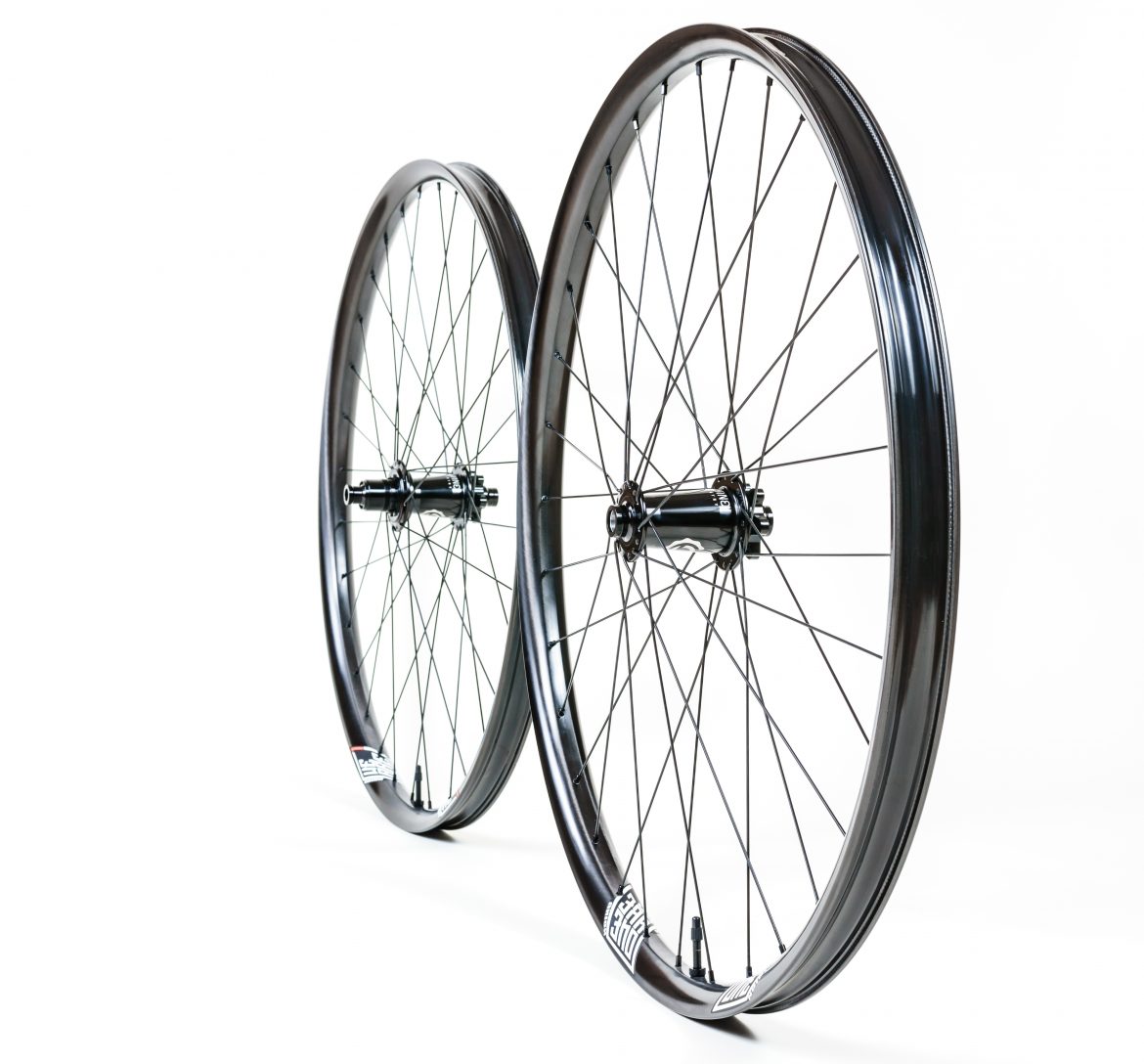
Can you tell us about the origin of your brand name?
The name We Are One stems from many angles. First, it is a play on carbon fiber being many layers and becoming one final part. Second, it was going to take a motto or name that was going to fuel my vision for a factory where all of our employees felt connected to the outcome. Thirdly, we wanted to be a more inclusive brand that was open to everyone and have everyone feel welcome and a part of what we do, through our products. So the name We Are One was born. Composites are our focus.
How do you describe the differences between the Faction (trail), Union (AM/enduro), and Strife (DH) rims?
Each of them has a very unique [carbon] layup. Starting off with the Faction, we work on rims based on internal widths for tires, as well as weight categories and how they fall within the bike spectrum. So, the Faction is our trail/all-mountain rim that’s good for a bike with up to 150mm of travel, running 2.3 to 2.5″ tires. It has a different nipple bed layup from the other two, and the lip of the rim has a different orientation of the fibers. It’s a little bit more of a compliant rim than the other two, and also it’s way lighter at 420g. So you cut a pretty good swath of meat out of that rim. It’s not the lightest trail rim, but it is pretty damn light for its strength. Pound for pound it’s one of our strongest rims because of the fiber density in that package.
The Union seems to be our flagship rim. It’s 80% of our business right now. It’s got a much wider rim lip at 4.5mm which is really good for anti-flatting. It also has a different-nipple bed layup and different rim package layup because it has so much more volume. Then, the actual fiber orientation in the bead seat area is different on that rim than any of our other rims. So that’s our enduro rim, meant to be raced with a 2.4 to 2.6″ tire. It’s got a lot of girth and it’s meant to take a beating for sure.
Then, the Strife is our downhill rim. It comes out of the Union mold. It’s the same shape dimensionally but we add more material in the nipple bed, and a different [fiber] orientation on the rim lip, as well as extra fiber in the bead-seat area. Each rim is quite unique and not too many characteristics transfer over. The Strife does get a little stiffer, and we use woven fibers to make it stronger without having the stiffness go way up.
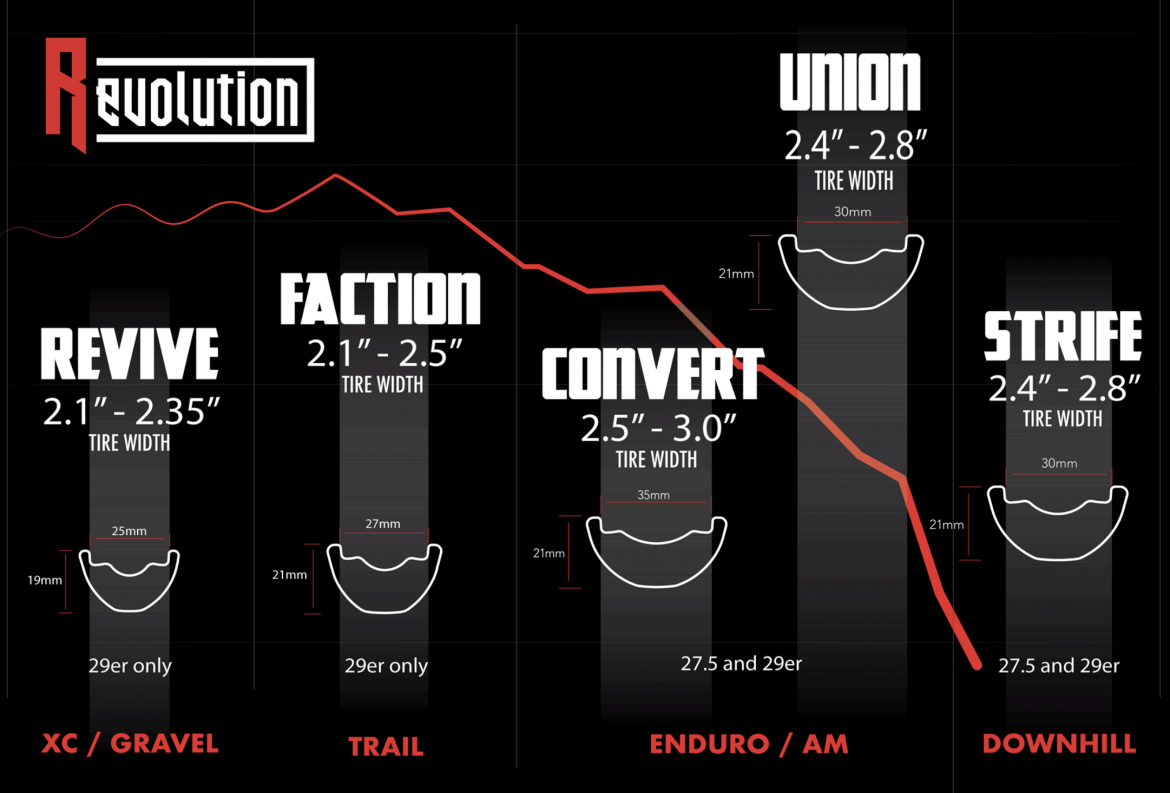
What’s your response when people say that carbon rims are too stiff?
I think that’s a valid point for someone who’s had them in the past. Even our first Agent rim was a very rigid rim. It’s based on a deeper cross-section, which you go for because you get more fibers to carry more load. It’s engineering 101. It makes sense to go that route in the early days. Now, if you look at rims that are performing really well, fiber density is more the game. Rather than having fibers on a horizontal or vertical plane carrying the load. I think everyone’s shrinking down to tighter packages and going denser, and we’re getting better longevity and much more compliant rims than we had in the past. Also, the availability of materials has significantly changed. A lot of companies are starting to pay attention to that.
When you say that there’s more fiber in the Union rim, what does that mean in terms of carbon layup?
It’s not such a big wide rim, so you’re able to put more fiber into that small dense area compared to a larger rim. If weight wasn’t a factor we could definitely make the Union and the Strife even denser, and have them even stronger, but weight is still the driving factor for a lot of people when they choose carbon fiber. For our company, weight isn’t our goal. Durability and strength are our goals, and a lot of people are starting to see their rim weights creep up closer to aluminum weights, but there’s definitely a lot of strength factors and gains to our rims over aluminum.
What is the main advantage of carbon rims over alloy?
It’s a difficult question. Aluminum is a homogenous structure. It doesn’t have any characteristics to it other than it’s got yield. It’s a malleable product, and it’s very reliant on the whole wheel system. So, tension, the number of spokes, and the type of aluminum are big factors. You can’t really tune that system. You can’t say, okay, I want that system to be more laterally stiff and less radially stiff. Or, I want it to have more give in this direction or that direction. You can’t really do much with that other than changing out your extrusions and trying to work on different structures to make it more rigid in a radial manner. I think that’s pretty much all you’re left with.
Whereas a carbon rim you’re able to tune in any direction, laterally or horizontally. You’re able to tune the ride, and how much stiffness is put into the rim. You’re able to tune what we call rebound. So, when you compress the rim, how fast does the rim come back to zero. You can’t tune that with aluminum. When you compress aluminum to a point it’s going to yield and give you a flat spot. It’s not going to snap back to its original state under large loads. It will fatigue the spokes and the system, and it needs to be trued and maintained. Whereas a carbon rim can have a major compression. It can shoot you out of a corner. A lot of people that ride our wheels say they’ve noticed that the wheels load up when they come into a corner, and it feels like you exit with more speed because the rim is actually snapping back to its original state. That energy does transfer into the ride.
There are a lot of claims about aluminum being better than carbon; I think a lot of those people haven’t ridden the new versions of carbon rims. I have yet to have anybody put carbon rims, especially ours, on their bike and say “this is not a performance increase. I don’t like these.”
When you mention rebound, do you have to test and consider tire rebound as well?
Yeah, when we do wheel testing it’s a super dynamic system. If you wanted to test the system, you’ve got suspension, frame flex, tire pressure, tension on the spokes, spoke count, rim design. All of that stuff comes into play for what the rider is going to feel. To test a completely dynamic system is extremely difficult. So, when we test we use the same tire every time so that we know the consistency is there.
Does We Are One do anything different with build, tune, or layup for front vs rear wheels?
We haven’t on our current models. We do tune each rim model differently. The Convert is going to ride much differently than the Union and so on. We have been playing with different rim widths front and rear all season, and last season as well. We’re working on something new that’s going to be a more rear and front specific setting. There’s definitely merit to that thinking. I’ve been running a Faction and a Union in the rear all summer, with the Convert upfront. So that’s a 35mm internal width up front on a 2.5″ tire, and a 2.5″ tire in the rear with 30mm and 27mm rims. We’ve cut some new prototype molds based on some thoughts I’ve had. I think a 35mm might be a little too wide. We cut it back and we’ve been working on a 33mm and a 29mm wide rim.
The thought process for us is that you can put a more dense fiber package into the rear which will make it stronger. The front rim can also be made wider so you get a better platform from the tire. We can also lighten the package up and make that front rim more compliant. We’re also playing with spoke count between 32 and 28 to see if that’s a big difference.
Can you share any teaser info with our readers about the new bike you all are building?
We’re going Super Boost. I prefer the 157mm spacing for a few different reasons. One thing we’re doing is taking advantage of Super Boost without widening the Q-factor up front. So, keeping the 73mm BB so the chain line is optimal. It takes advantage of what Super Boost is made for, and that’s chain line. I think if bike companies used it [Super Boost] the way we’re using it, the benefit would be 100% obvious.
How are you all doing with the current bike buying boom?
In the grand scheme of things we’re still a small manufacturer. I’ve never seen a plan for our growth where we’re a big player, like DT Swiss or Mavic or even Enve. That’s not what I want. I want a company that people want to be involved with. We did se a boost this year no doubt. We got to a point where we had an eight week lead time, and we’ve had to adjust. But, for the wheels side of things I don’t want to go much larger than what we are. We’d lose the feel, the vibe, and what we are as a company would be lost in that growth. I want to keep it where we’re at and keep the product in at a high quality. If people have to wait, so be it. We know that people who wait are going to get the best product.
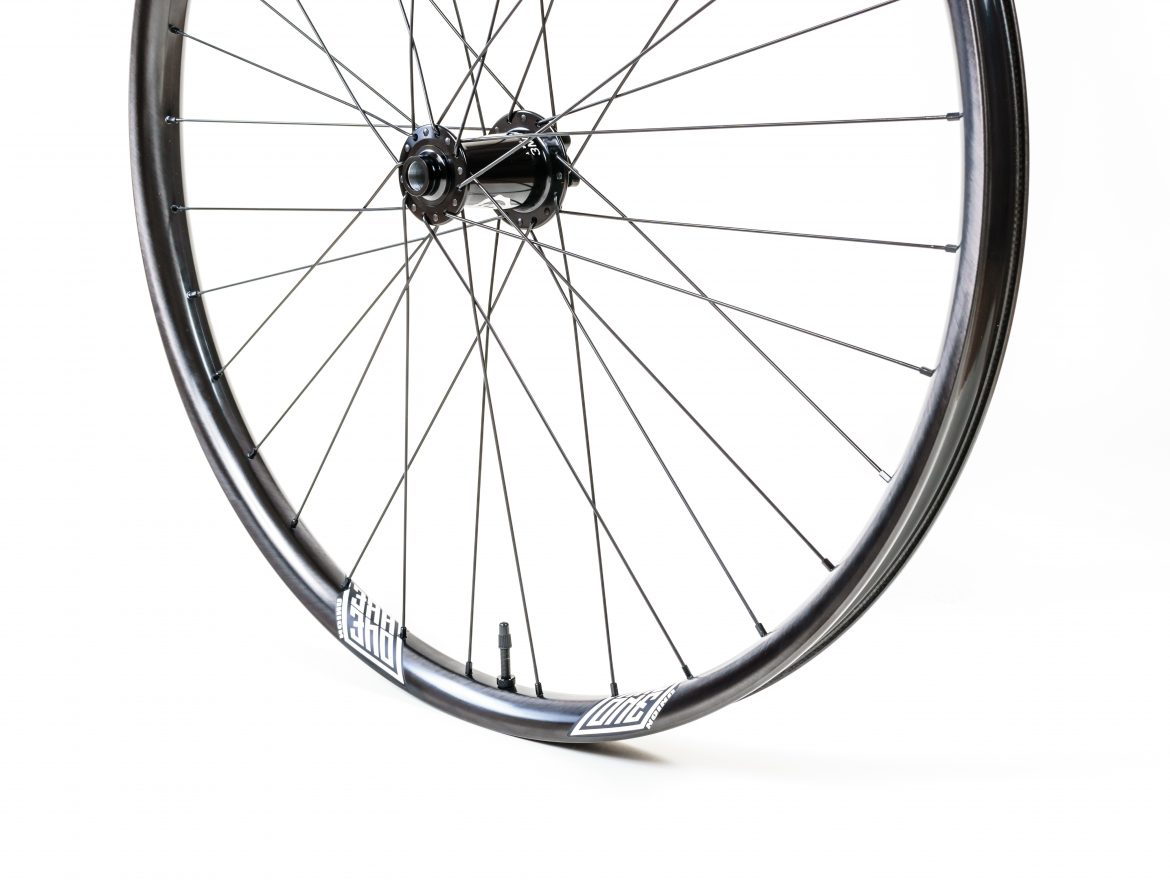
Are you all also working on hubs?
We have a new CNC lathe that we’re using to make parts for the bike. We’ve kicked it around, there’s no doubt about it. With a lot of patents coming up the hub market is going to be pretty saturated in the next couple of years. I’m not sure if we’ll enter into that market. We have a great relationship with Industry Nine right now. We really respect what they do and we’ve formed a good working relationship.
Do you all play with different spoke lacing patterns?
We have started to play with more lacing patterns and hole counts for sure. We have always default built our 29″ wheels in a 2x pattern and our 27.5″ wheels in a 3x pattern. The biggest reason to going to 2x for 29 was a bit more lateral stiffness and to cut some spoke weight out of the wheels. We are currently testing 28 to 32 hole patterns in our test lab and we are trying to put data to which is better and what gains or losses might come from one over the other. This is all working towards our newest product in the wheel side of things.
How did you decide to use alloy vs brass nipples? How about spoke sourcing?
The companies doing anodization work have far exceeded the specifications for aluminum. 95% of our wheels are built with aluminum nipples and we’ve never seen a wheel fail due to spokes pulling through, or the threads caving in, or corrosion. We’ve got wheels out there with the same aluminum nipples after four years. I was a skeptic at first, but for the amount of weight, you save that far out [in terms of rotating mass] I think it’s perfectly fine.
For spokes, we stick with Sapim. We have had issues with sourcing in the past, and we stick with Sapim because they support us and I think they have the best nipple for a carbon rim out there. They’ve got all the spokes we’d ever need.
What do you think about center lock vs. six-bolt brake rotor mounts?
I personally like center lock. It’s easier to remove the rotor, easier to put it on, the hubs are lighter. But, something’s going on in the industry right now. Chris King has switched to center lock for their whole platform, and I’ve heard rumors that other hub manufacturers moving to centerlock as well.
And, the question we have to ask any wheel company: what are your thoughts on tire inserts?
It’s an interesting situation. So, we know that the best thing you could possibly put in your tire to avoid rim strikes is air. More pressure is less rim strikes. It’s fool proof, and works every single time.
The other thing is, why lighten up the wheel to reduce the rotational weight, to reduce the amount of time it takes to get you up to speed, and make all of these benefits, then ram in something that removes all of that weight benefit? Also, by putting something in there the air volume is decreased. You’re [now] reliant on the foam to do what? Is it just to stop rim strikes? Is it giving a better or stiffer casing? How does all of that affect the movement of the rim? With the pressure from the insert, the rim doesn’t bend and move as well as it should. We’ve seen them [inserts] have negative impacts on the longevity of a rim, where the rim is taking more hits, and if we focused on a little more PSI we would have less.
Who are some of the top athletes supported by We Are One for 2021?
Rae Morrison, Remy Morton, Hannah Bergemann, Lewis Buchanan, and a lot of local riders and ambassadors. Our goal this year is to find people who are doing good things in their community and then we just surprise them with the wheel setup.
That’s it from We Are One for now, but stay tuned for a podcast with Dustin Adams once the new frame launches. If there are other gear questions you want answers to or brands you would like us to interview please let us know in the comments below.
0 Comments